Why is the Color of PCB Mostly Green?
What is the green layer on PCB?
The printed circuit board we usually see is green. In fact, the printed circuit board also presents other colors, such as white, blue, black and red. The most common green part is the outer layer of resin called solder resist film or solder resist oil. This is a kind of hardening resin with color pigment, which is applied to the circuit board by screen printing.
The surface of the PCB is covered by a welding mask. This material reduces the action of the polymer and protects the copper rail from oxidation, moisture and particle damage. The covering layer avoids the formation of solder cross between appropriate applications, which are close again and cause a short circuit.
Top reasons why most PCBs are green in color
1. Green can relieve visual fatigue and facilitate inspection
In the early days, due to technical limitations, quality inspection relied on workers to manually inspect circuit boards with bare eyes. It's a tiring job to use your eyes to see tiny circuits all day. Neuroscientists and psychologists agree that the wavelength of green light has a relaxing effect on the body and can reduce fatigue. Therefore, manufacturers believe that making PCB green helps workers detect and find errors. When detecting green PCB board, it is easier to find the difference between circuit track, electrode and screen. In other words, the higher the contrast, the easier it is to find errors. With the development of science and technology, PCB manufacturers now use flying needle technology and automatic optical inspection (AOI) to complete these tasks, which is very effective in detecting finished products.
2. Physical properties of green solder resist film
The color green represents chlorine, which mainly exists in the solder resist oil. The glass epoxy resin originally used to produce PCB solder coating is green. Green is bright magenta, with the lowest manufacturing cost; Therefore, it is still the standard color of modern circuit boards.
The traditional green welding mask seems to be the only color that can keep the 0.1mm welding mask consistent (red, blue and yellow for more than 4mm, 0.12mm in diameter, then white and black, usually only 0.15mm). IC needs to weld mask barrier} and micro pitch parts because they are important in avoiding solder span. The color of the circuit board will not affect the efficiency of the circuit board but will affect the resolution, that is, the accuracy of the circuit board. Although the green circuit board has no effect on the working mode of the device, the green welding mask does. The green solder resist film of 0.1mm has better solder resist effect than other colors.
3. Influence of military on PCB development
Some people believe that green was chosen as the standard color because of the army. The US military has studied the PCB color and found that green is the most effective color, especially when tested under adverse conditions. Because of their testing, the military decided to take the green printed circuit board as the standard.
4. The price of green PCB is relatively cheap
Glass epoxy resin, used as solder resist film, is a natural green. Green has become the customary standard in the industry. Therefore, even if there are solder resist coatings of different colors, many manufacturers still choose green. Green welding mask materials are more cost-effective because of their versatility. In short, green PCB is a universal and cheaper choice.
Other available circuit board colors
Blue PCB board has novel color and looks high-grade; Lack of hardness, easy to scratch, and defective products will increase during production; Large fluidity, easy to accumulate and uneven; The plug hole is difficult and easy to flow out after the plughole; The baking board takes a long time and is easy to get dirty. It is easy to stick the film print after packaging.
Black PCBs and white PCBs can be helpful on some special occasions. For example, most LED light boards use a white PCB. The reason is that the colour of white will reflect light and absorb less heat.
The advantage of black PCB is to reduce floodlight and light reflection. In this way, the display contrast of each pixel of the assembled dot matrix screen will be high. Secondly, it can also avoid the reflection of external light and improve the display effect of the screen, especially for outdoor applications.

Solder Mask Color | Solder Mask Type | Minimum Webbing (mils) | Coverage (mils) (X, Fig.9) |
Green | PSR4000 HFX | 3 | 2 |
PSR4000 LDI | 3 | 2 |
PSR4000 BN | 3 | 2 |
Blue | PSR4000 HFX | 3 | 2 |
PSR4000 LDI | 3 | 2 |
PSR4000 BN | 3 | 2 |
Red | PSR4000 HFX | 3 | 2 |
PSR4000 LDI | 3 | 2 |
PSR4000 BN | 3 | 2 |
Black | PSR4000 HFX | 5 | 3 |
PSR4000 LDI | 5 | 3 |
PSR4000 MP | 5 | 3 |
Brown | PSR4000 BN | 5 | 3 |
White | PSR4000 BN | 6 | 3 |
The Colors Of Printing Circuit Boards
The color of a PCB surface is actually the color of solder resist, which can prevent the wrong soldering of components, prolong the service life of devices, and prevent the oxidation and corrosion of devices. If you know something about electronic products, you will find that the color of a printed circuit board is green in most cases.
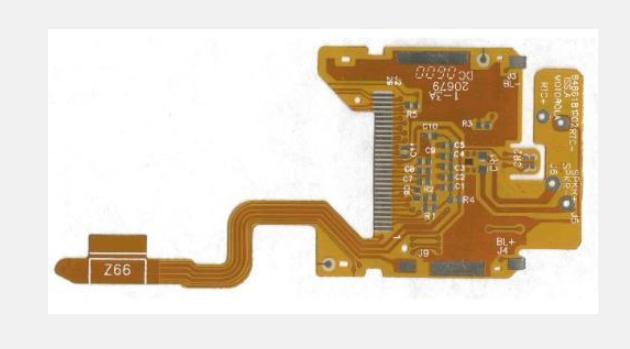
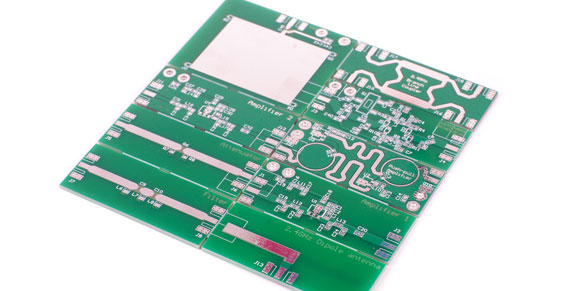
This is mainly because the green solder mask process is the most mature and simple, and the green board is also more environmentally friendly. In addition to green, PCB company also has printing circuit boards in other colors, such as white, yellow, red, blue, matte colors, and even chrysanthemum, purple, black, bright green, etc. White is the necessary color that is used to make lamps and lanterns, and other colors are used to distinguish product samples. From R&D to product landing, the experimental board may be purple, the keyboard will be red, and the computer internal board will be black depending on the different uses of printing circuit boards, which will be distinguished and marked by different colors. As for the green oil, its solder resist ink has the longest history, lowest price, and most popularity.
The Advantages Of Green PCB
1. Several processes of board making and laminating need to be carried in the yellow light room, where the green PCB has the best visual effect;
2. In SMT patch processing, green is more easily for the bottom plate to be recognized by the instrument as optical positioning and calibration are required in the steps of tinning, patching, and AOI calibration;
3. Some inspections rely on workers' observation (but now flying probe tester has replaced this labor in most cases), which needs workers to keep staring at the board under strong light, and green is friendly to eyes;
4. Green printing circuit boards are relatively environmentally friendly, and no toxic gas will be released when the waste boards are recycled at high temperatures. Other colors, such as blue and black, have weak electrical conductivity, which may lead to short circuits as these colors are doped with cobalt and carbon. In addition, colors like black, purple, and blue are too dark, which will increase the difficulty of the inspection and maintenance of the motherboard, and the process is not easy to control.
Taking the black board as an example, the black board is most likely to cause obvious color differences and high PCB defect rates due to problems in the production process and the ratio of raw materials. What's more, the traces of the black circuit board is hard to identify, which will increase the difficulty of maintenance and debugging. Therefore, PCB factories hardly use black printed circuit board. Even the fields of military industry and industrial control all use green printed circuit boards in their products with extremely high-quality requirements. To sum up, it is not difficult for us to understand why the color of a printed circuit board is mostly green.